Your Guide to CNC Machines: Tips & Trends
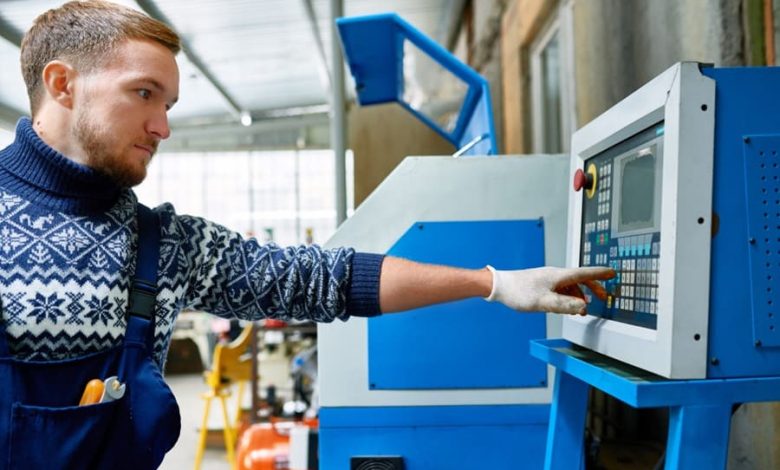
As you step into the dynamic world of modern manufacturing, you’re likely to encounter the transformative power of CNC machines. These powerhouses of precision machining are not just buzzwords; they are pivotal in the way products are crafted today. With the burgeoning adoption of CNC technology, understanding how it can enhance your production capabilities is essential. In this guide, you’ll unearth the latest tips and trends that could be the difference between good and exceptional manufacturing outcomes. Embrace the journey into an era where accuracy meets innovation, and let’s delve into the core of CNC’s influence in the industry.
Understanding CNC Machines and Their Capabilities
At the heart of automated manufacturing lies the powerhouse known as CNC machines, or Computer Numerical Control equipment. The term might sound technical, but these machines are what make modern manufacturing marvels possible. Let’s peel back the layers on how CNC machining works and delve into the capabilities that set it apart from traditional manufacturing methods.
Imagine having the ability to transform digital blueprints into precise physical components with just the touch of a button. That’s the core function of CNC machinery that you can find for example on www.megaplot.com. With advanced software, these machines interpret complex designs and perform various operations such as drilling, cutting, and carving with unfaltering precision. One could almost liken a CNC machine to a skilled craftsman – but one that can work tirelessly, repeatedly, and without a single error.
- Automated Precision: CNC machines operate with exactness that human hands might find challenging to match.
- Repeatability: Create one masterpiece or a thousand duplicates; CNC equipment ensures each piece is identical.
- Speed: Accelerate production timelines significantly, as machines work faster than manual methods.
- Versatility: Capable of working with a breadth of materials and performing numerous operations, flexibility is a key advantage.
Beyond these capabilities, the benefits of leveraging computer numerical control are immense. From optimizing production workflows to achieving consistency in manufacturing, CNC equipment has revolutionized how industries construct a wide array of products. Here’s a table that illustrates the transformative impact of CNC equipment in setting new manufacturing standards.
Capability | Advantage | Industry Application |
High Precision | Minimized error rate in production | Aerospace and Defense |
Complex Design Interpretation | Execution of intricate design features | Consumer Electronics |
Multifunctionality | One machine for drilling, cutting, and more | Automotive Manufacturing |
Enhanced Speed | Faster time-to-market for products | Medical Device Production |
The transformation from a digital concept to a tangible, meticulously crafted item entails a comprehension of CNC machines and their capabilities. Your knowledge of automated manufacturing opens up a new realm of possibilities where efficiency and accuracy are just the beginning. With CNC machining, you’re not just producing; you’re innovating in a field where precision is the norm and excellence is the expectation.
The Importance of Precision in Automated Manufacturing
When you consider the world of automated manufacturing, the precision brought about by CNC machines is non-negotiable. The intricate dance of CNC tooling and machinery results in products that boast remarkable accuracy, symmetry, and consistency. Here is where precision machining steps in as the ultimate arbiter, ensuring that each component meets exact specifications, time and time again.
Imagine a scenario where a mere fraction of a millimeter mismatch could result in a catastrophic failure of a crucial aerospace component, or where a slight deviation in a medical device impedes its critical function. Your reliance on CNC precision isn’t just about quality; it’s about safety, functionality, and trust in the end product. Advanced CNC tooling contributes significantly to maintaining the tight tolerances that these sectors demand.
The benefits that stem from the utilization of CNC machines in complex and precision-critical projects are manifold. Not only do you get to witness an elevation in product quality but also the satisfaction of delivering consistent results that align perfectly to predetermined benchmarks, every single time. The following table underscores the pivotal role of precision in different aspects of manufacturing.
Aspect of Manufacturing | Role of Precision Machining | Benefits |
Product Quality | Ensures products are made to exact design specs | Enhanced performance and reliability |
Repeatability | Achieves the same tight tolerances across multiple runs | Avoids variability and reduces waste |
Complex Projects | Manages intricate designs with accuracy | Opens up possibilities for innovation and complex solutions |
Speed and Efficiency | Speeds up production without compromising on quality | Faster time-to-market and increased throughput |
Cost Savings | Reduces material waste and rework | Overall reduction in manufacturing costs |
As you navigate through the terrain of automated manufacturing, remember that the capabilities of your CNC machines are inextricably linked to the precision that your projects necessitate. Whether it’s sophisticated CNC tooling or the expertise behind the console, precision machining remains a pillar on which the structural integrity of manufactured goods is built. And for you, it is the source of confidence that each product hitting the market under your purview isn’t just made, but crafted, with unparalleled precision.
Advancements in CNC Technology
As you delve deeper into the world of precision machining, it’s crucial to stay abreast of the latest CNC technology advancements. Recent years have seen significant strides in CNC milling and CNC turning, developments which have the potential to dramatically reshape the way industries function. Let’s explore some of the exciting innovations that can set your manufacturing processes apart.
The evolution of CNC technology has led to the invention of new materials specifically formulated for CNC milling procedures. These materials are designed to withstand the high-stress environment of machining while maintaining the integrity of the finished product. Furthermore, the incorporation of advanced composites has opened up new possibilities for strength and durability in machined parts.
Enhancements in machine efficiency cannot go unnoticed in the current landscape of CNC technology. Manufacturers are continually implementing energy-saving features and optimizing machine operations to ensure the most cost-effective production runs. This focus on energy efficiency not only reduces operational costs but also contributes to a more sustainable manufacturing process.
The software and hardware associated with CNC machines are also getting smarter. Intuitive interfaces and adaptive control systems are making it easier than ever to perform complex tasks with little margin for error. Such advancements in CNC software are pivotal in reducing the learning curve for operators, ensuring that high-quality results are achievable regardless of one’s experience level in machining.
Below is a comparative overview of traditional vs. updated CNC technology features:
Feature | Traditional CNC Technology | Updated CNC Technology |
Materials Used | Standard alloys & plastics | Advanced composites & custom formulations |
Energy Efficiency | Standard consumption | Enhanced energy-saving designs |
Software & Hardware | Basic interfaces and programming requirements | Intuitive software and adaptive hardware systems |
These advancements are not just for the future; they are available right now, ready to be integrated into your manufacturing operations. Embracing the new wave of CNC technologies can lead to more efficient production lines, higher quality products, and a significant edge over competitors who stick to outdated equipment and processes. When considering your next investment into CNC technology, keep these improvements in mind to ensure your operations are not just current but also future-ready.
Introduction to CNC Programming and Software
The pulse of modern manufacturing beats with the rhythm set by sophisticated machinery, and at the heart of this mechanized dance is CNC programming. As you delve into the intricacies of automated manufacturing, understanding the role of CNC software in transforming digital blueprints into precise, tangible parts is paramount. It’s a digital language that instructs the very moves of CNC machines, crafting complex components with the finesse of a skilled artisan.
In your journey through the world of CNC, you’ll quickly learn that CNC programming is as critical to the machining process as the machine itself. The software used in these processes acts like the brain of the operation, meticulously guiding the machine’s every action. Whether you are milling, turning, or cutting, CNC software stands as your reliable partner, ensuring each product meets exact specifications with stellar efficiency. Embracing this technology means you’re empowering your manufacturing capabilities with the ability to repeat tasks with unfailing precision—key to staying competitive in today’s fast-moving market.
This glimpse into CNC programming is just the beginning. As you further explore the realm of automated manufacturing, you’ll find that mastering CNC software opens up a world of possibilities, enabling you to produce high-quality parts with the kind of speed and accuracy that was once unthinkable. Remember, it’s not just about the machines; it’s the harmonious blend of top-tier programming and cutting-edge hardware that sets the stage for manufacturing excellence.